
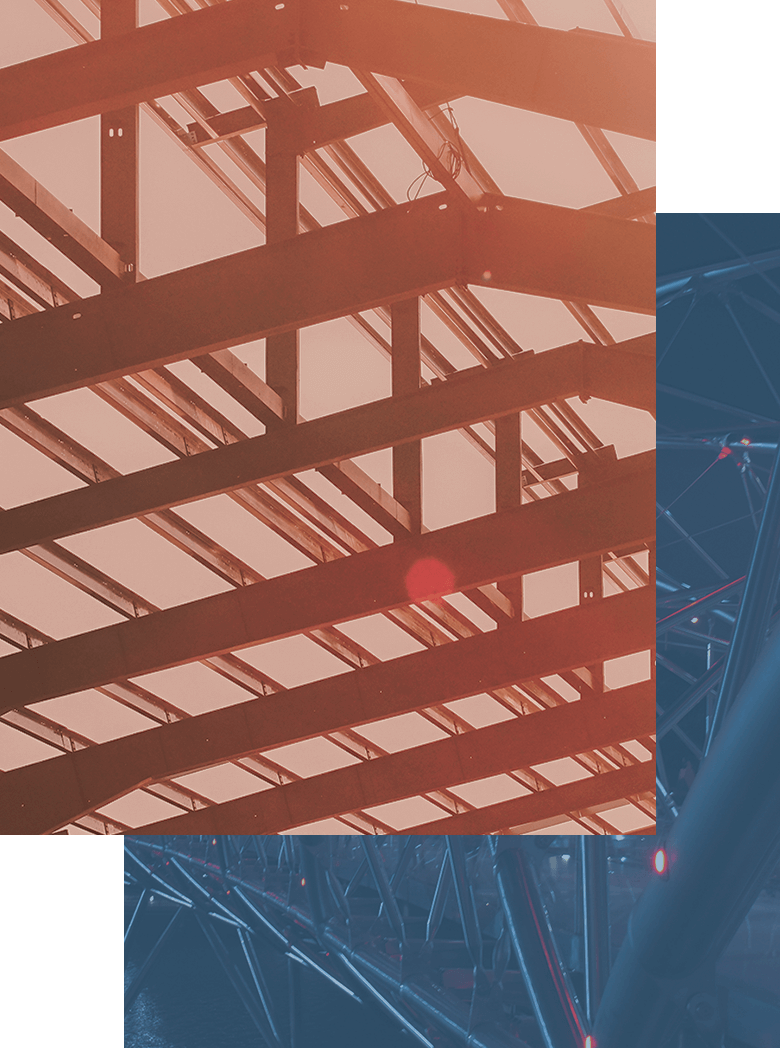
Steel Division
JCL is leading the way in terms of raw steel processing and production in India. Our steel operations are based out of Sidiginamola Village, Bellary District, Karnataka.
Our belief in harnessing resources and energy efficiently and optimally has translated into using the waste gases produced in our sponge iron processing to set up a 15 MW power plant focusing on waste heat recovery. We also own and operate a 6 lakh tonnes per annum iron ore pelletization plant which was set up by capitalizing on the shortage of high-grade iron ore lumps. Our iron-ore pelletization facility agglomerates ore used to make iron. We have also installed an induction furnace with secondary refining and continuous casting capabilities to produce steel billets. Additionally, our sponge iron plant with a capacity of 1,80,000 MT per annum serves as the nucleus for our steel processing house.
The forementioned capabilities means that JCL now has a completely backward integrated steel production plant in place, allowing us to be cost-competitive and extremely process efficient.
Products
Iron Ore Pellets
As a pioneer when it comes to the production of iron ore pellets, JCL uses Grate-Kiln technology to produce pellets from iron ore fines. This process facilitates production of superior grade feed material for Sponge Iron, also known as Direct Reduced Iron (DRI), Metalized Iron, or Hot Briquetted Iron.
During the production process, iron ore fines are wet grinded, then dewatered. Dewatering is a process whereby fine sized concentrate is mixed with binder and other additives. This results in several green coloured balls that are formed in the disc pelletizers.
These iron pellets are then heated, dried, and indurated. Once complete, these are cooled and put into stockpiles. Most iron ore pellets produced are used in-house to produce Sponge Iron. Using this technique, we optimise resources and reuse waste material to maximise our output. The pellet plat production capacity at JCL is 0.6 million tons per annum.
Sponge Iron
Sponge iron is produced by reducing iron ore in the form of pellets using non-coking coal in a rotary kiln. The coal acts as fuel as well as a reducing agent when oxygen is removed from the ore to produce the sponge like properties. Since the reduction takes place in the solid phase only, the output is called direct reduction. The finished product has pores like a sponge due to the removal of oxygen molecules. Sponge iron formed through the reduction of iron ore to metallic iron occurs due to a reaction with carbon in the form of coal at approximately 1,100 degrees Celsius.
Sponge iron is used in the iron and steel industry as a substitute for scrap in induction and electrical arc furnaces. Over the years, the shortage of expensive melting scrap has made sponge iron a significant raw material for manufacturing high quality steel.
In India, the abundance of iron ore deposits has led to Sponge Iron’s absorption across industries. The vast use of ore lumps and fines has led to the country becoming the largest producer of sponge iron in the world.
At JCL, we adhere to a Quality Assurance Plan (QAP) defined by a qualified technical team. Our qualified chemical engineers visit customer sites to provide technical support for any technical or operational issues faced by them.